THE CHALLENGE
Meat producer, Edwards of Conwy wanted to speed up bacon label production and cut the costs associated with applying their old style cardboard sleeves. These particular sleeves were machine applied, pre-glued and folded, with the finished result lacking in on-shelf appeal. In the factory, production was labour intensive and slow, with frequent application errors. The cardboard sleeves also had to be coded separately, resulting in further downtime and wasted sleeves on a daily basis. The company also wanted to begin reducing their carbon footprint so opting for linerless was the first major step in offsetting their emissions. The end goal was to source a linerless label applicator that could streamline operations for a speedier, more cost effective and ‘greener’ process for labelling their bacon products.
ABOUT EDWARDS OF CONWY
Edwards of Conwy is based in Conwy, North Wales and was founded by Master Butcher, Leuan Edwards. After learning ‘The Art of Butchery’ in both Switzerland and Holland, Leuan at the age of 20, opened a butchers shop in 1984 and this award-winning establishment is still a thriving business today. The shop lies at the very core of their wider business operations for showcasing their finest work and offers the perfect platform for launching new products to their loyal customers. In 2004, Leuan built a small production unit under the same brand, specialising in supplying major UK supermarkets, for export and the foodservice sector. Since this time, business operations have gone from strength to strength with recent market research demonstrating that Edwards of Conwy is now the number one premium sausage brand in Wales. A success story built on passion and dedication for consistently producing high quality meat by adopting as many traditional methods and recipes as possible. They employ 65 people and plan to double business operations over the next 5 years.
THE SOLUTION
The Machine
Edwards of Conwy decided to purchase a Nobac 500R ready meal / slideable sleever for applying the sleeves to their bacon packs.
Key Features: Nobac 500R – ready meal & slideable sleever machine
- Inline machine designed for maximum flexibility
- Eliminates the need to turn the packs
- Capable of applying 100mm – 225mm wide slideable sleeves
- Pack speeds of up to 65ppm are achievable
- Linerless labels allow for more labels per roll, resulting in longer runs and increased uptime
- With automated sleeving, customers can benefit from reduced costs and labour
- Wasted printed labels on changeovers minimised by printing at point of application
- Eliminate wasteful and non-recyclable backing paper
- Increase in production efficiency
The Labels
The slideable sleeves are produced by our linerless printer, Reflex Labels.
Key Features of the slideable sleeve
- Aesthetically pleasing
- Attractive presentation at POS
- Fully recyclable – no need to landfill
- Based on a traditional cardboard sleeve format yet comes supplied on a roll (traditional cardboard sleeving methods involve manual application)
- Slideable sleeve material up to 300gsm
- Increased surface print area: top and underside
- Linerless reels weigh up to 40% less and take up 40% less space when comparing to self-adhesive labels / those carrying backing paper
- Reduced costs and labour
- Quicker machine application
- Less storage space required
SUCCESS STORY
Edwards of Conwy report significant cost savings since production has shifted to linerless and purchasing the Nobac 500R applicator. In the factory environment, the Nobac 500R takes up less space and turnaround for applying the sleeves is 40% faster. Previously, their old style sleeves had to be coded separately, on a separate machine. Coding is now handled by the Nobac 500 so downtime and waste is significantly reduced. Lead times for orders are now much improved. The company also utilises 50% less paper than their previous labelling method. Changes to label artwork are also quicker and less costly with our approved linerless printer, Reflex Labels. Overall, a much reduced carbon footprint. Their bacon is sold across all major retailers within Wales with a nationwide distribution handled via Ocado. Excellent sales are reported to date with plans to buy two further machines within the next 18 months. The machines will meet growing customer demand and satisfy objectives to roll out linerless label application to all of their sausage and bacon products; widening their distribution network to Tesco, Asda, JS Supermarket, Morrisons and Spar.
For further information, contact Marketing at Ravenwood +44(0)1284 749144.
Linerless Label Printer for producing the sleeves, Reflex Labels.
Visit Edwards of Conwy Edwards of Conwy.
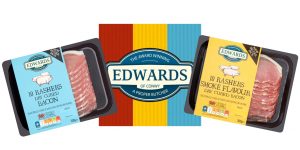
Edwards of Conwy linerless sleeves featured on bacon packs…